Maintaining the tires of a rubber tired gantry crane is crucial for ensuring safe and efficient operations, prolonging tire life, and minimizing downtime due to tire-related issues. Rubber tired gantry cranes are widely used in container terminals, ports, and intermodal yards for lifting and transporting containers, and their tires play a vital role in supporting heavy loads and navigating various terrain conditions. Proper tire maintenance practices are essential to optimize performance, reduce operating costs, and enhance overall operational productivity. Let’s delve into the key steps and strategies for maintaining the tires of a rubber tired gantry crane:
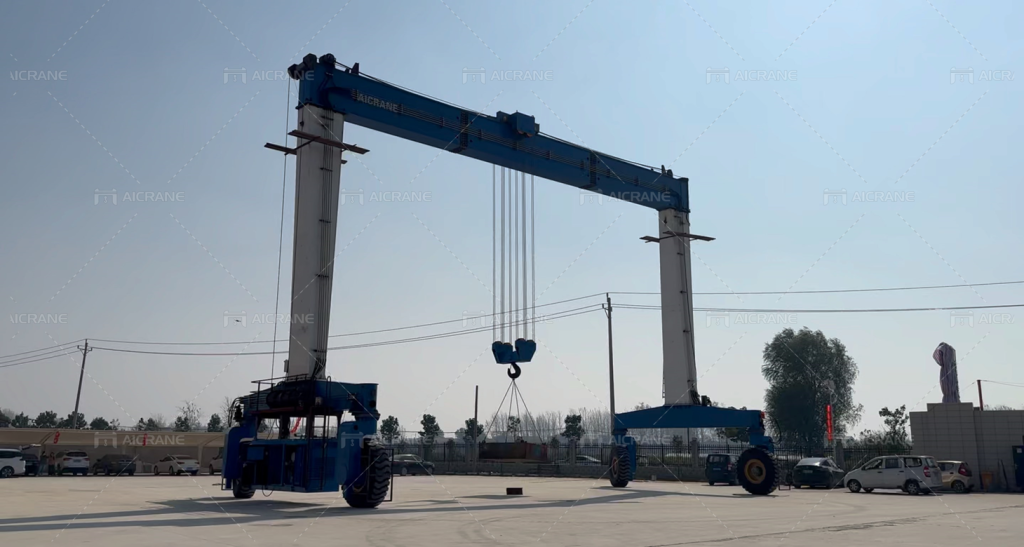
Regular Inspections
Start by conducting regular visual inspections of the rubber tired mobile gantry crane tires to identify signs of wear, damage, or abnormalities. Inspect the tire treads, sidewalls, inflation levels, and overall condition. Look for cuts, tears, punctures, bulges, uneven wear patterns, embedded objects, and signs of deterioration. Inspections should be performed daily or as part of routine maintenance checks.
Tire Pressure Monitoring
Maintain proper tire inflation pressures according to the manufacturer’s specifications and guidelines. Improper tire inflation can lead to accelerated tire wear, reduced traction, decreased fuel efficiency, and increased risk of tire blowouts. Use a tire pressure gauge to measure and adjust tire pressures regularly, especially after temperature changes or heavy load operations.
Wheel Alignment Checks
Ensure that the rubber tired gantry crane’s wheels are properly aligned to prevent uneven tire wear and premature tire failure. Misaligned wheels can cause excessive tire scrubbing, sidewall damage, and steering issues. Conduct wheel alignment checks using laser alignment tools or alignment indicators to verify alignment angles (toe, camber, caster) and make adjustments as needed.
Load Distribution and Handling Practices
Optimize load distribution and handling practices to reduce tire stress and wear. Avoid overloading the rubber tired gantry crane beyond its rated capacity, distribute loads evenly across tires, and minimize sudden stops, sharp turns, and aggressive maneuvers that can strain tires. Implement proper lifting and handling techniques to minimize impact forces on tires during container handling operations.
Tire Rotation Schedule
Implement a regular tire rotation schedule to promote even tire wear and extend tire life. Rotate tires at specified intervals or based on wear patterns to ensure that tires wear uniformly across all positions. Follow the manufacturer’s recommendations for tire rotation patterns (front-to-back, side-to-side) to maintain balanced tire wear.
Cleanliness and Debris Removal
Keep the rubber tired gantry crane tires and wheel rims clean from dirt, debris, grease, and contaminants that can cause tire damage and corrosion. Use water, mild detergent, and brushes to clean tires regularly, especially after operating in dusty or muddy conditions. Remove lodged debris, rocks, and foreign objects from tire treads and sidewalls to prevent punctures and cuts.
Tire Repairs and Replacements
Promptly repair any tire damage, punctures, or leaks to prevent air loss and maintain tire integrity. Use proper tire repair techniques, patches, and sealants recommended by tire manufacturers. Replace worn-out or damaged tires with new tires of the correct size, load rating, and tread pattern to ensure safe and reliable performance.
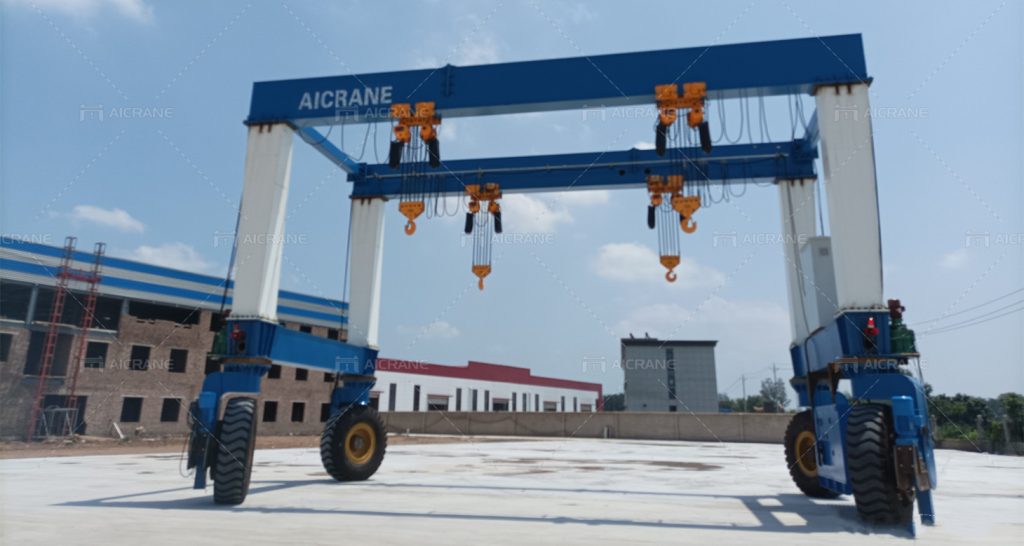
Temperature and Weather Considerations
Be mindful of temperature and weather conditions that can affect tire performance and longevity. Extreme heat or cold can impact tire pressures, rubber compounds, and traction levels. Monitor tire pressures regularly during temperature fluctuations and adjust as needed. Store spare tires in a climate-controlled environment to preserve tire quality.
Training and Operator Awareness
Provide comprehensive training to rubber tired gantry crane operators on proper tire maintenance practices, load handling techniques, and safe operating procedures. Emphasize the importance of regular tire inspections, inflation checks, and reporting any tire issues or abnormalities. Encourage operators to avoid excessive speed, sharp turns, and aggressive maneuvers that can stress tires.
Data Collection and Analysis
Utilize tire management systems, sensors, and data collection tools to monitor tire performance, track tire wear trends, and analyze tire-related data. Collect data on tire pressures, temperatures, wear rates, rotations, and maintenance history to identify patterns, optimize maintenance schedules, and make informed decisions regarding tire replacements or repairs.
Collaboration with Tire Suppliers
Work closely with tire suppliers, manufacturers, and service providers to access technical support, tire maintenance recommendations, and expertise. Collaborate with tire specialists to select the most suitable tires for rubber tired gantry crane applications, monitor tire performance, and implement proactive maintenance strategies.
Record Keeping and Documentation
Maintain accurate records, logs, and documentation of tire maintenance activities, inspections, repairs, replacements, and performance indicators. Keep track of tire serial numbers, sizes, brands, and specifications for inventory management and warranty purposes. Document tire-related incidents, issues, and corrective actions taken for future reference.
In conclusion, effective tire maintenance for rubber tired gantry cranes (RTGs) involves a comprehensive approach that includes regular inspections, tire pressure monitoring, wheel alignment checks, load distribution practices, tire rotations, cleanliness, repairs, operator training, data analysis, collaboration with gantry crane suppliers, and diligent record-keeping. By implementing proactive tire maintenance strategies and adhering to manufacturer recommendations, operators can maximize tire lifespan, minimize downtime, enhance safety, and optimize rubber tired gantry crane performance in container handling operations.